Cornell University desired to create a unique residential experience for first year and sophomore students that would strengthen their sense of belonging and foster camaraderie. In responding to their desire, the 776,000-square foot, 2,000-bed North Campus Residential Expansion student life complex is designed to promote this student interaction.
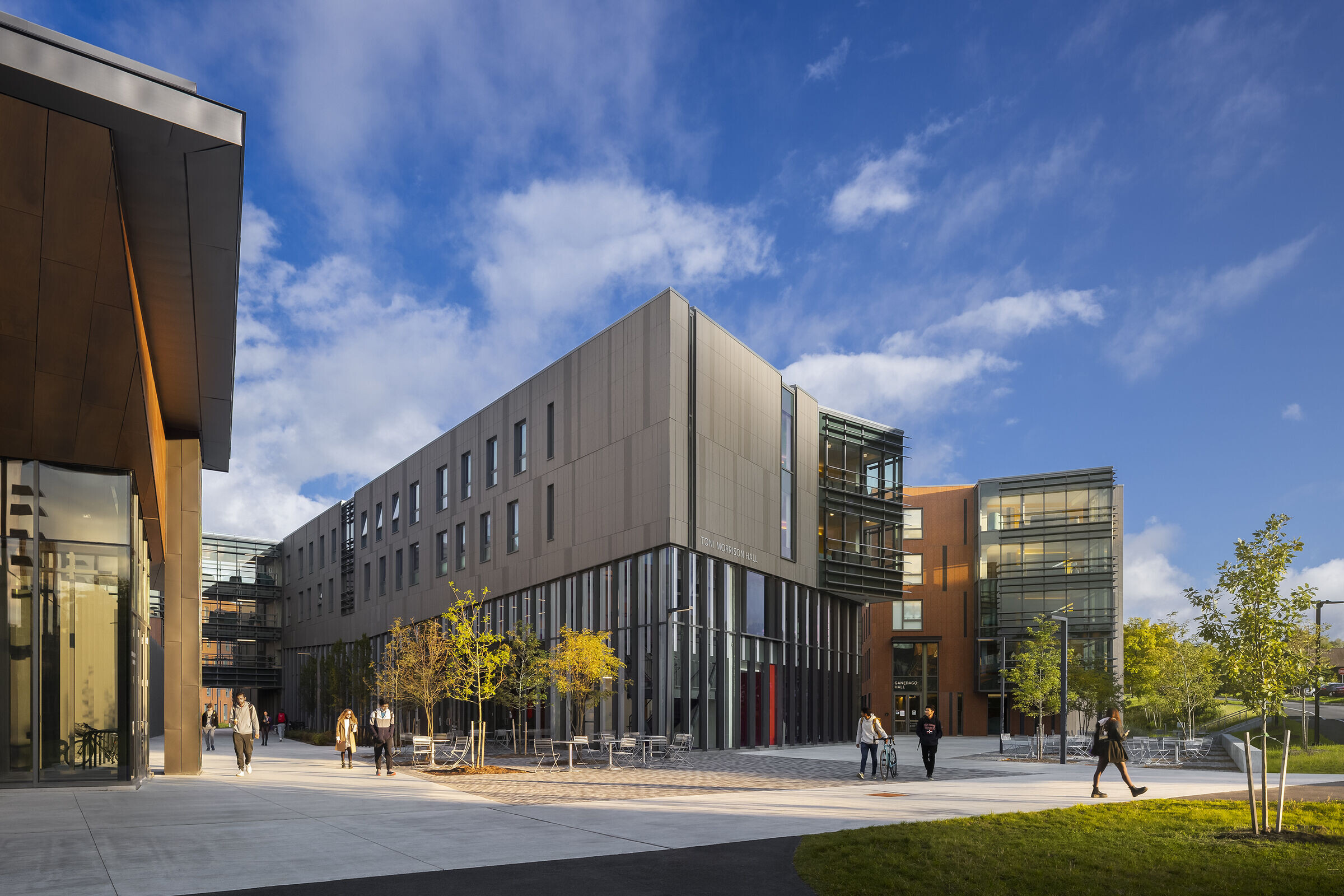
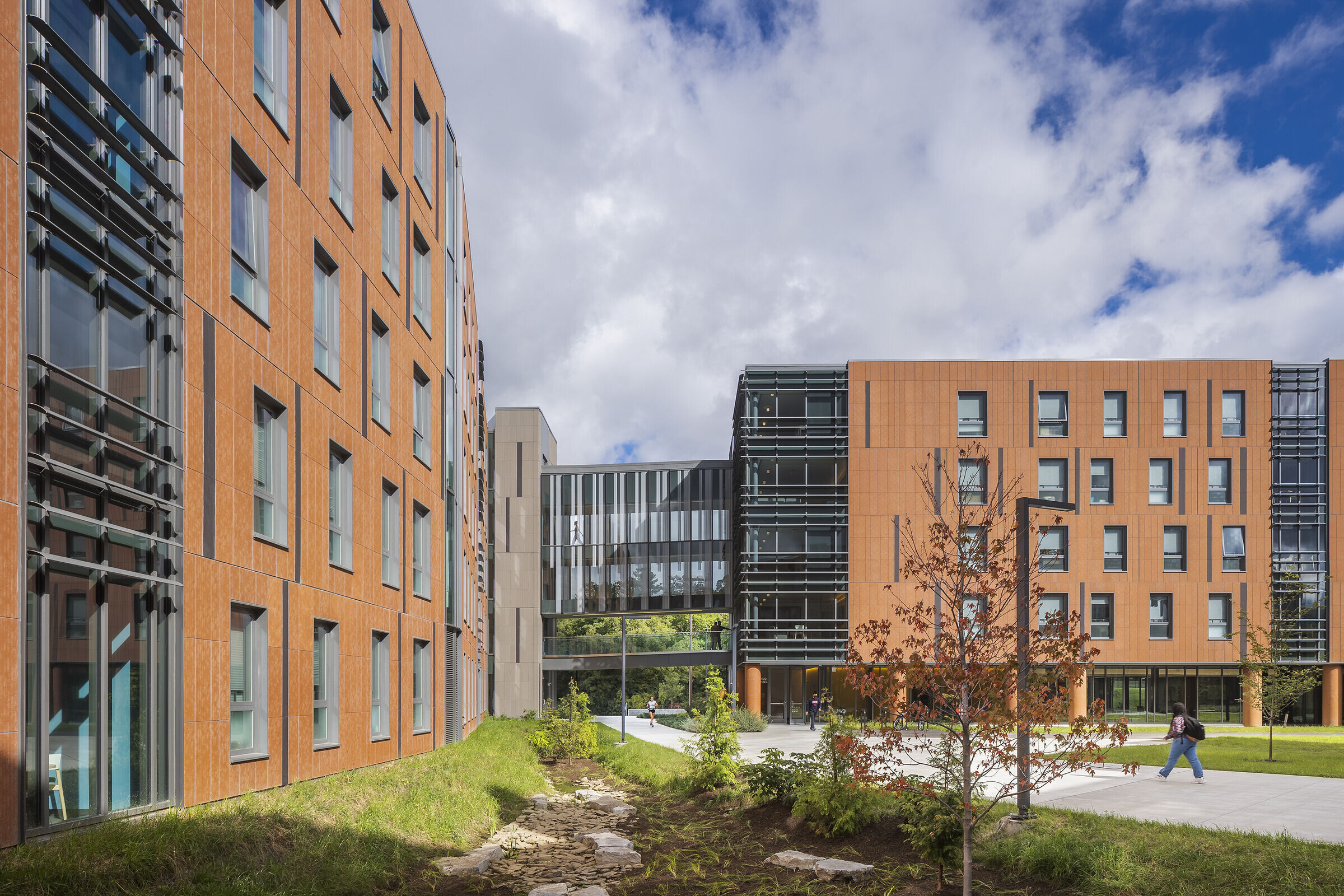
The ground floor with its open transparent colonnade is home to social lounges, community kitchens, offices, cafes, and gaming rooms. These spaces are highly visible and accessible and promote student interaction and activity. At the heart of the complex is the 1000-seat Marche’ themed dining experience, this is the largest social collector that attracts students campus wide. Additionally, the residential complexes are arranged around outdoor landscaped courtyards- an exterior social room for those students living adjacent to it.
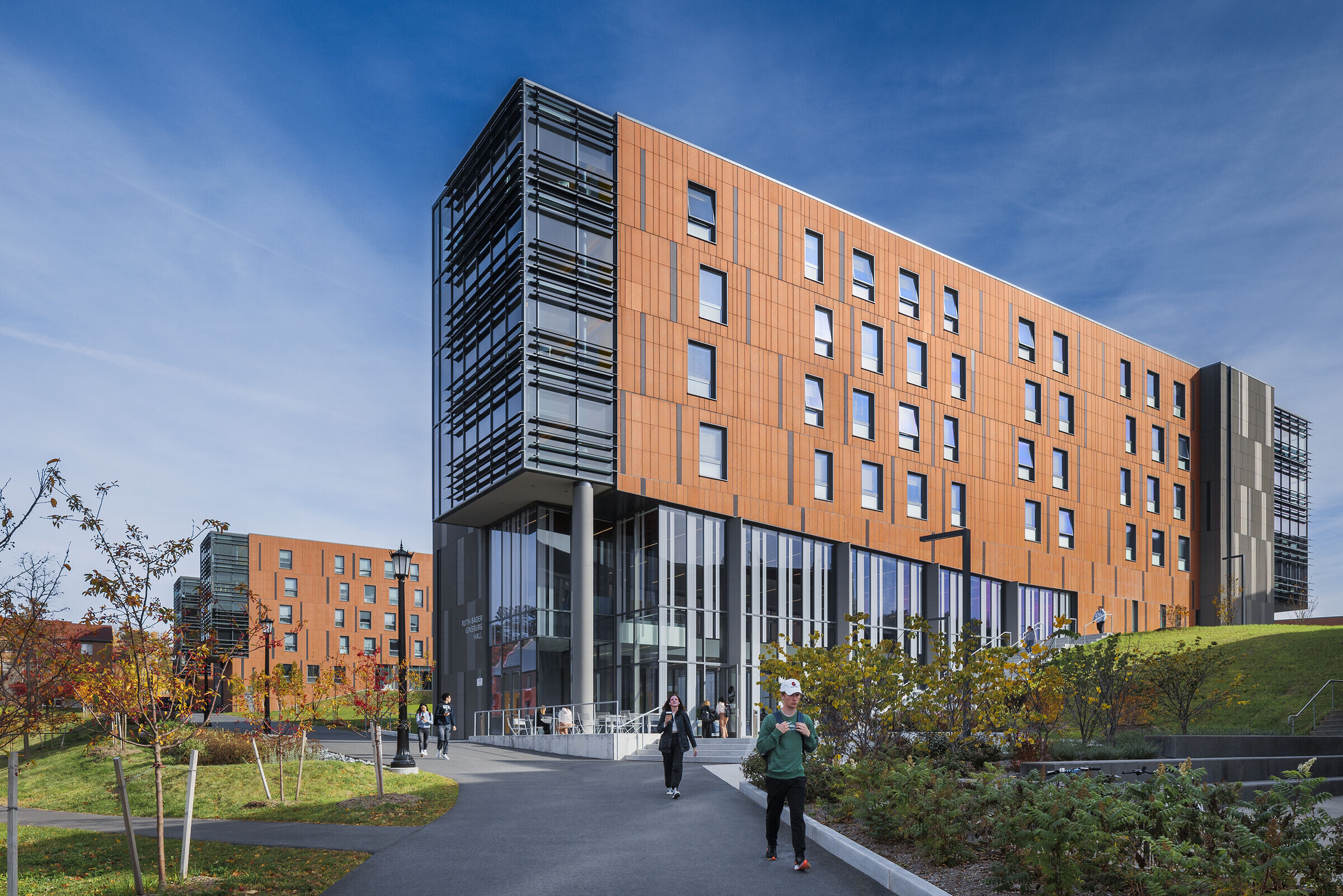
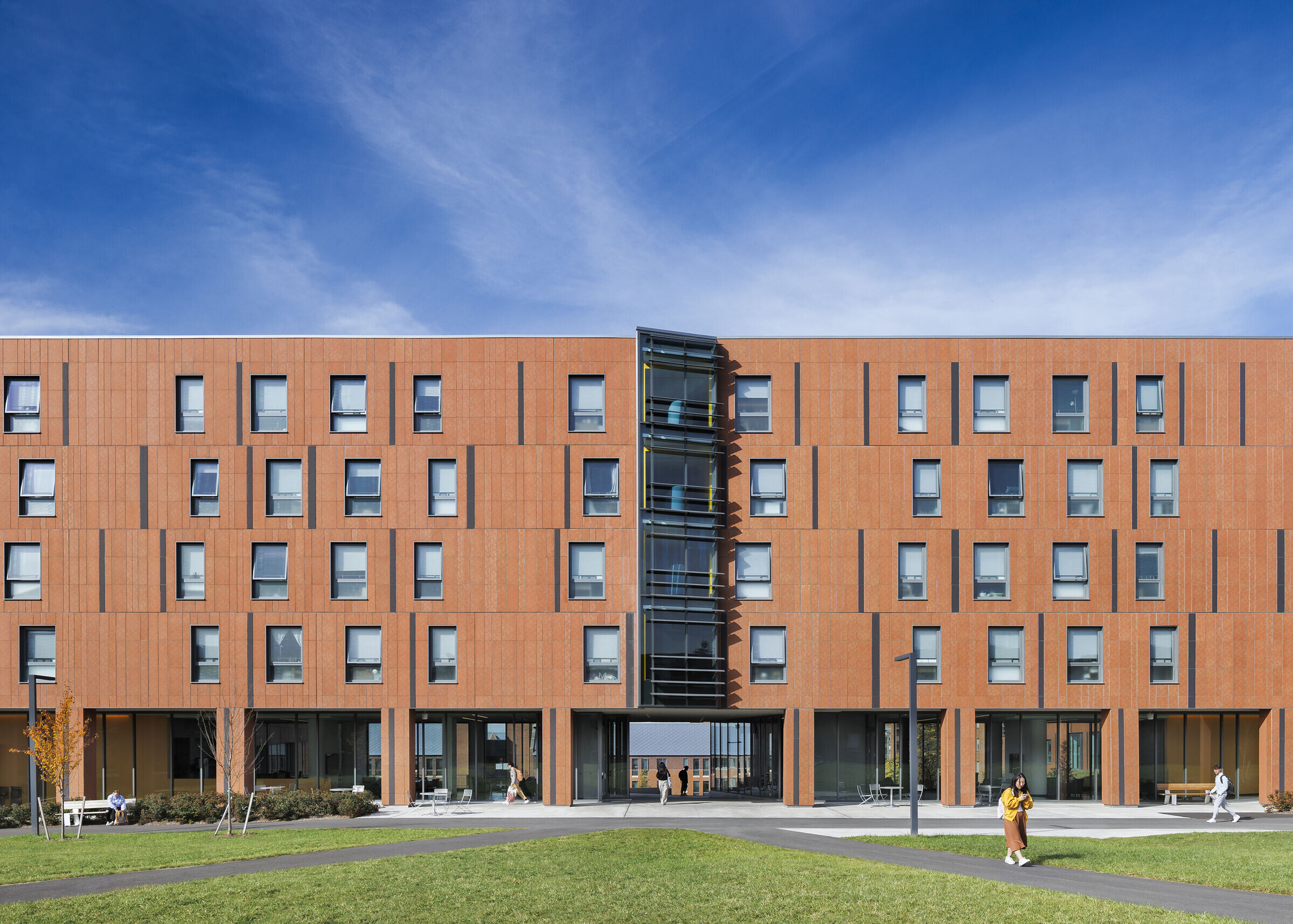
Each of the residential courtyards are unique and respond to its immediate context and topography. 3, 4 & 5-story buildings are arranged on both sites to create open and interlocking courtyard spaces that are contextual in scale & character, and are sited to enhance the overall campus plan by reinforcing the campus pedestrian network and minimizing traffic and parking.
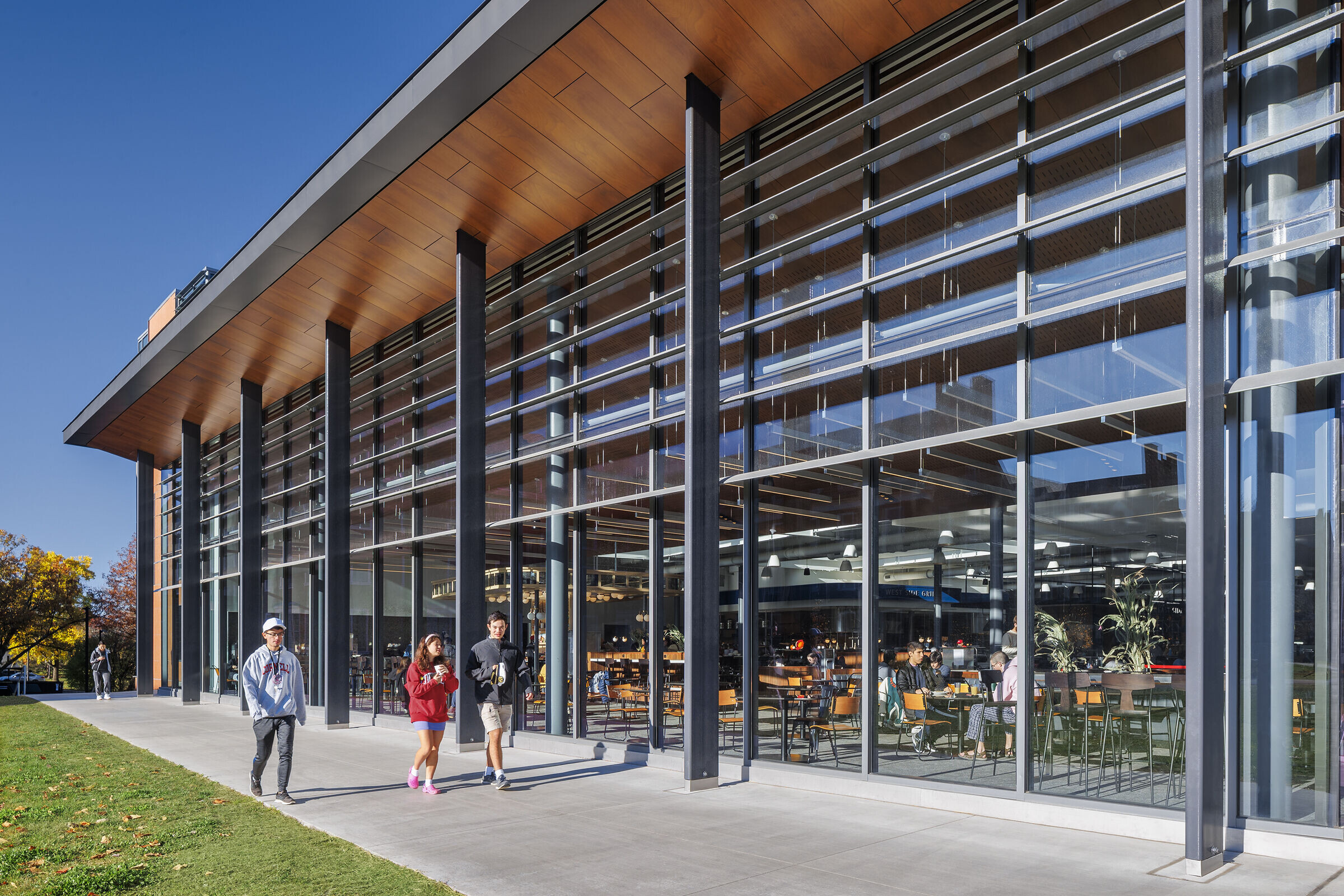
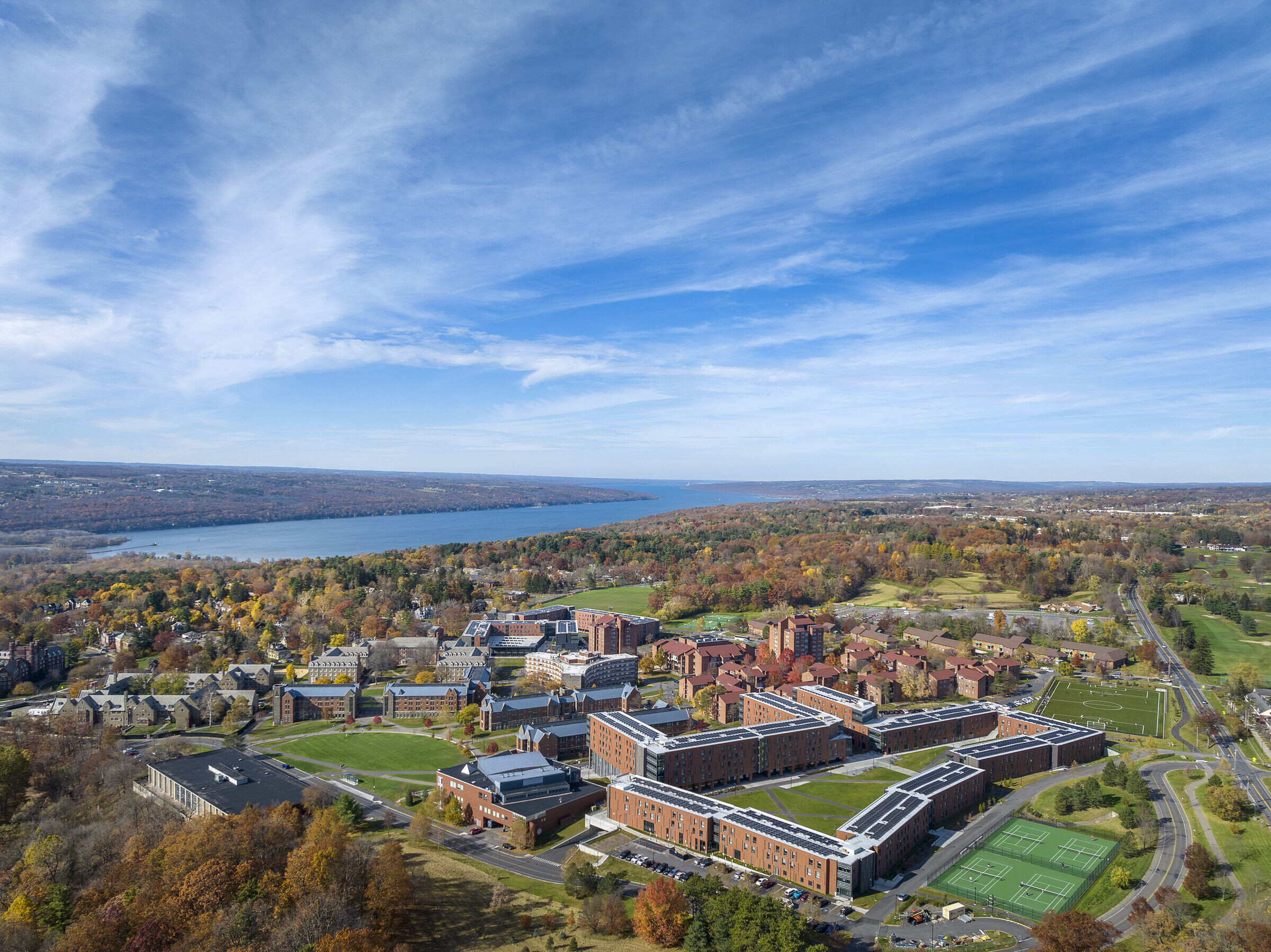
The precast building facades are designed as a modern interpretation of the existing brick and stone masonry buildings found elsewhere on the north precinct of the Cornell campus. This robustly constructed wall is composed of running patterns of red and grey terracotta tiles with staggered arrangements of punched windows. These walls are interrupted at corners and building ends by multi-story glazed curtain wall openings further reinforcing the social connectedness between inside and out.
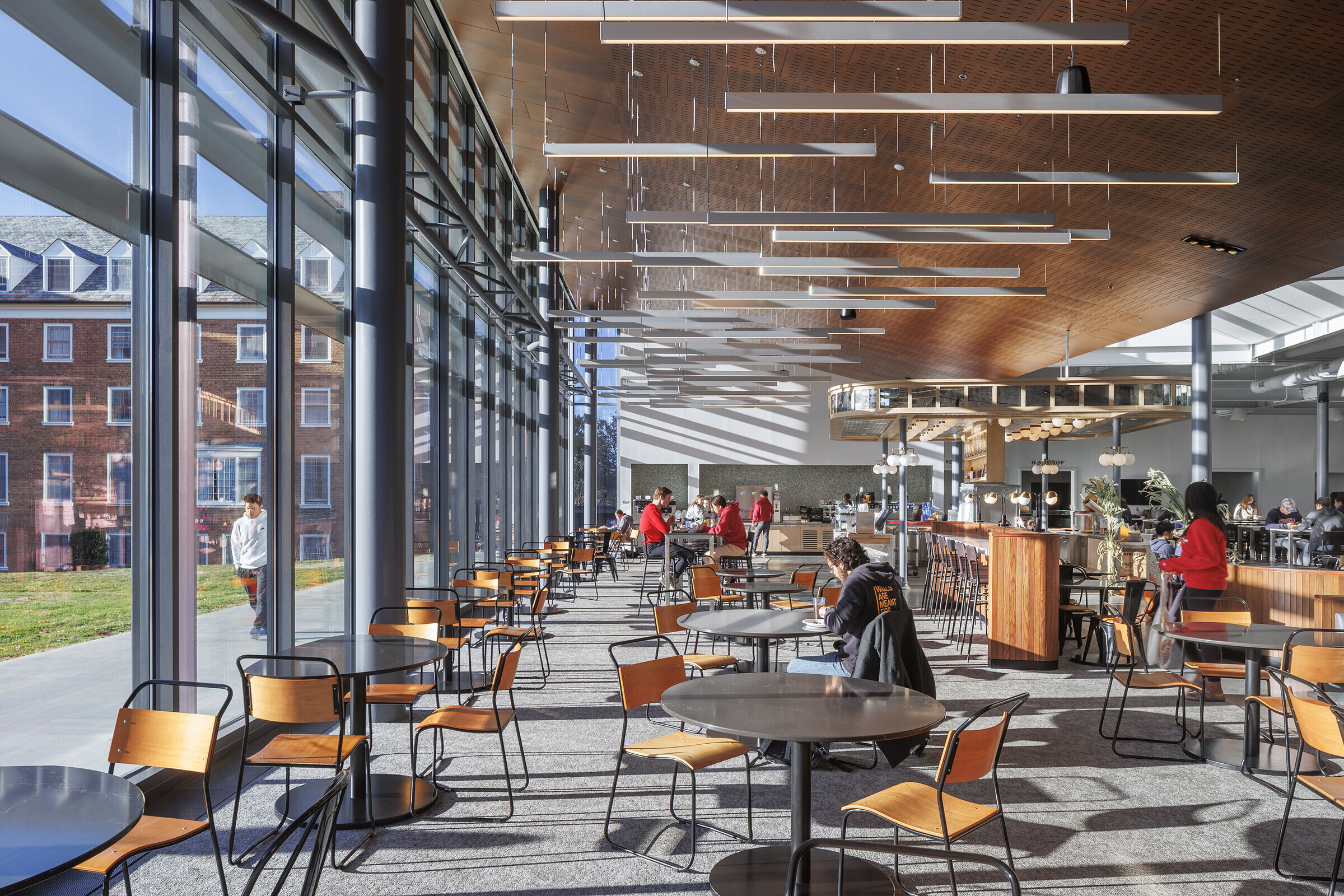
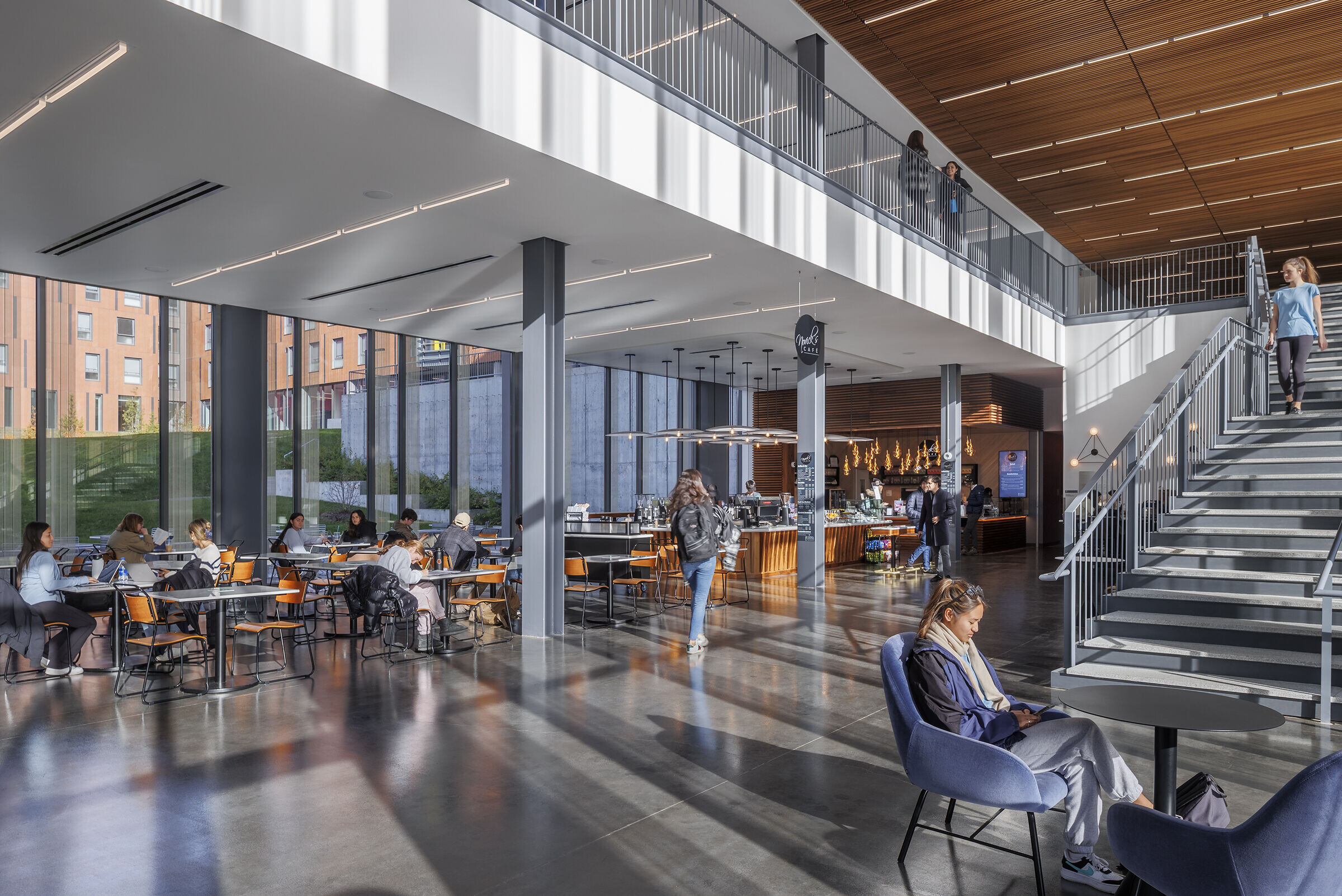
The key challenge of this project was schedule. Cornell had increased its first- and second-year student class sizes and needed to provide those students with housing. To meet an aggressive completion date, the design and construction team created an innovative prefabrication process whereby a portion of the structure, the exterior wall envelope and bathrooms were fabricated in a factory while the site and foundation work commenced. Given the overall size of the project, this allowed the construction schedule to be condensed because construction work was happening simultaneously and allowed the team to meet the completion date.
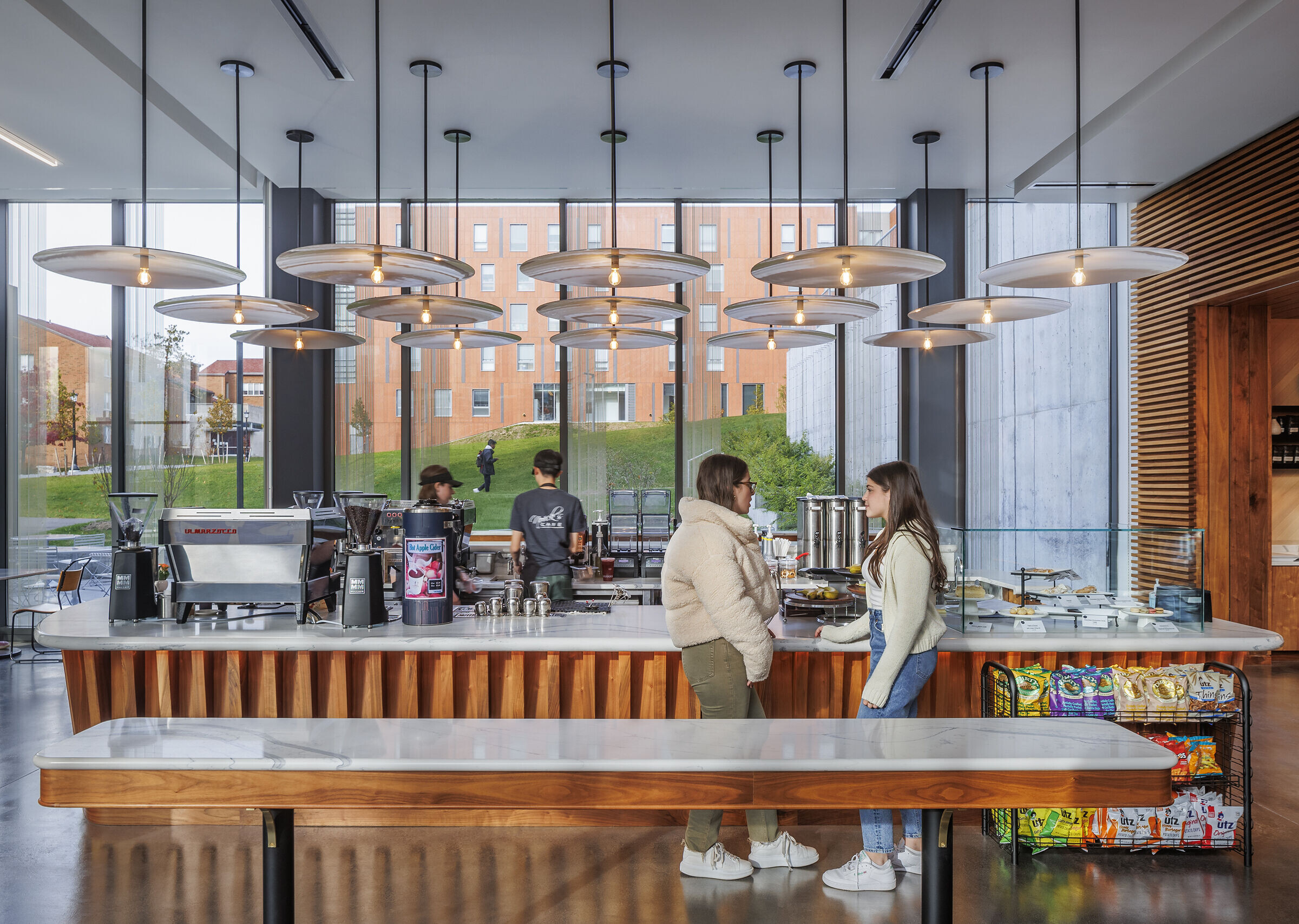
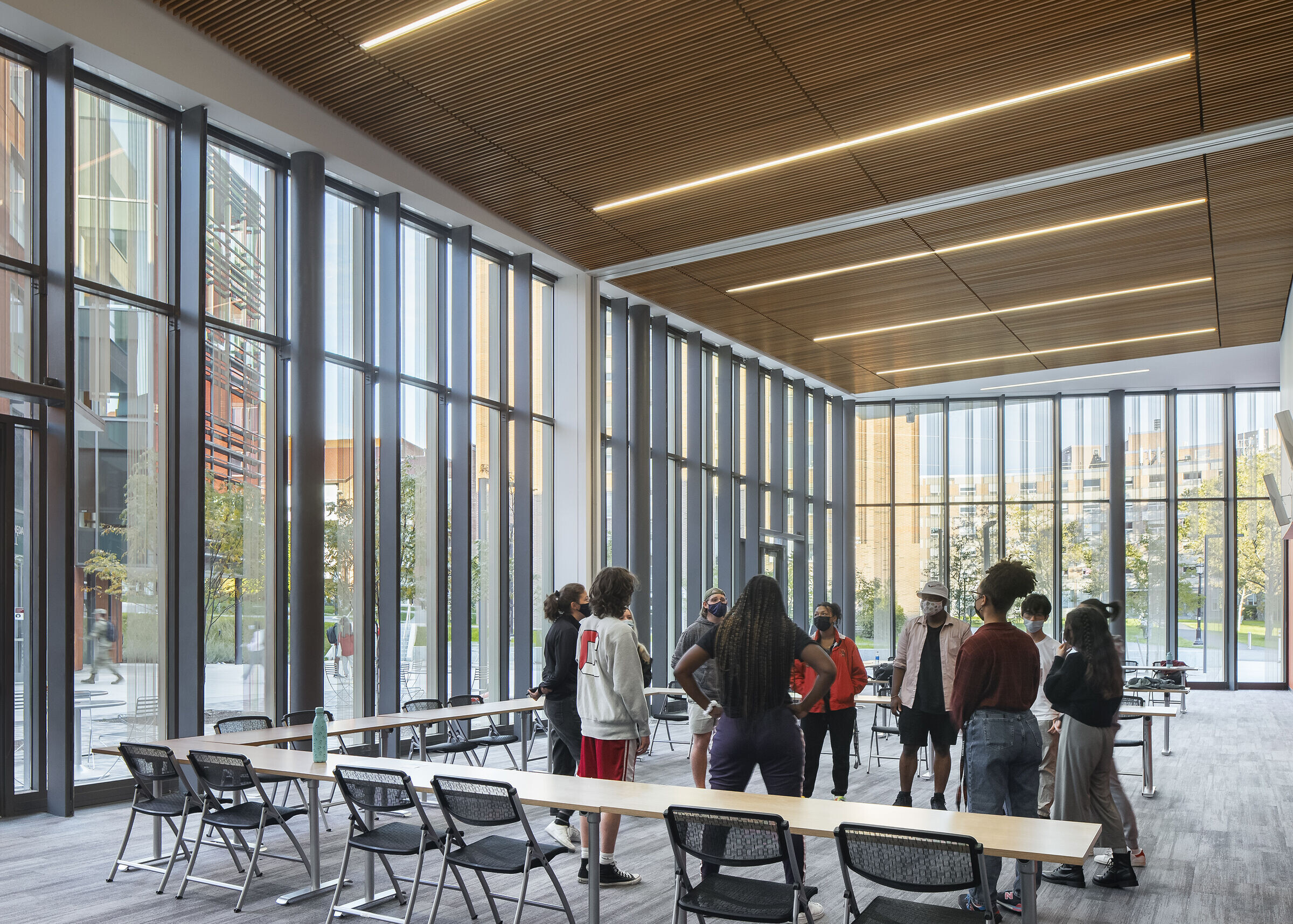
The building uses a precast girder and hollow core structural slab system which reduced the structural erection time. The building uses an insulated exterior precast panel that produces a highly efficient thermal envelope and a finish surface both on the exterior and interior wall surfaces reducing time in erection and finishing. The project organized the residential units into suite rooms with private bathrooms. As a result, there were hundreds of bathrooms. Constructing the bathrooms off site in a factory and transporting them to the site to be slid onto the floor plate with final plumbing and electrical connections reduced on-site construction time significantly.
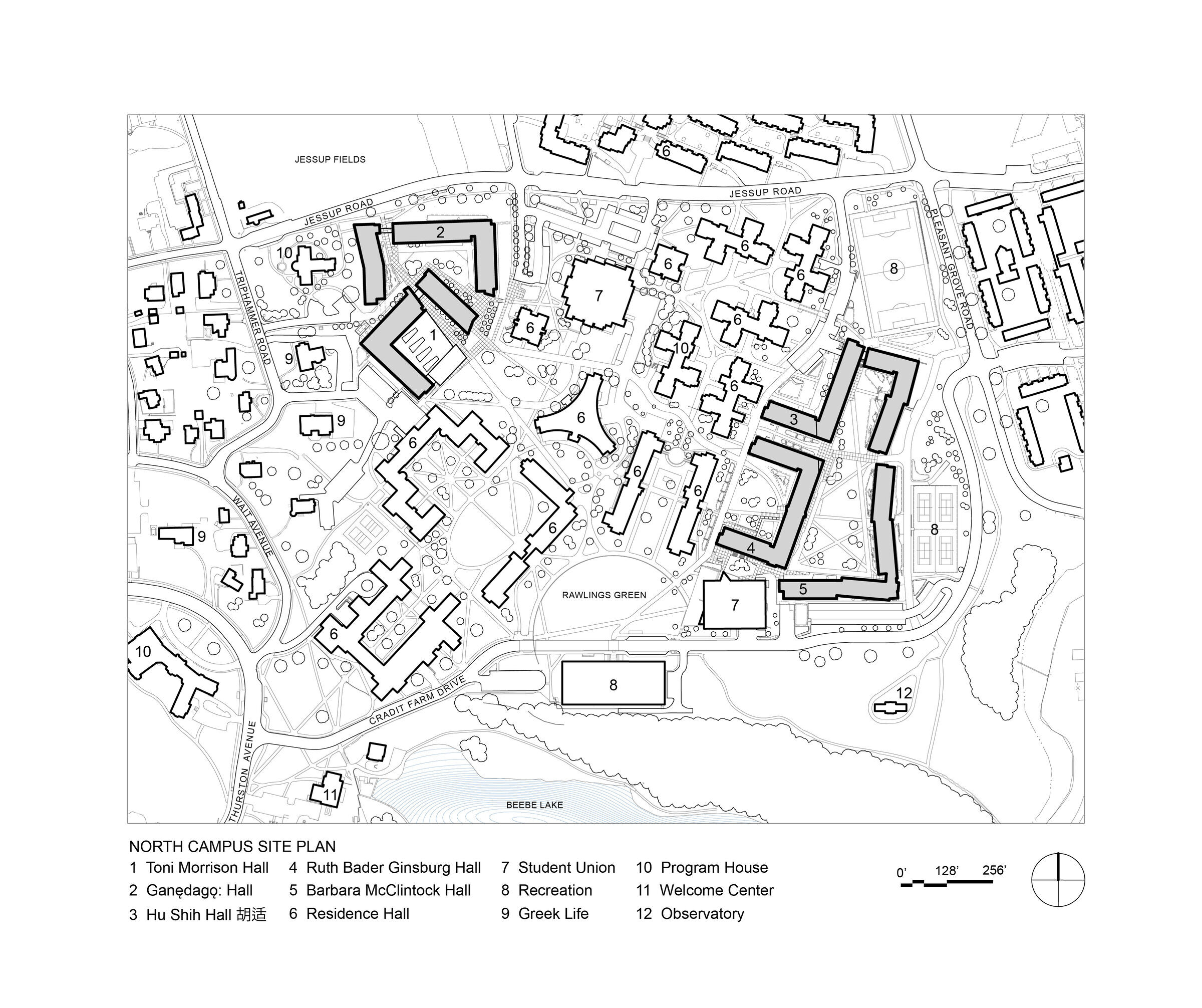
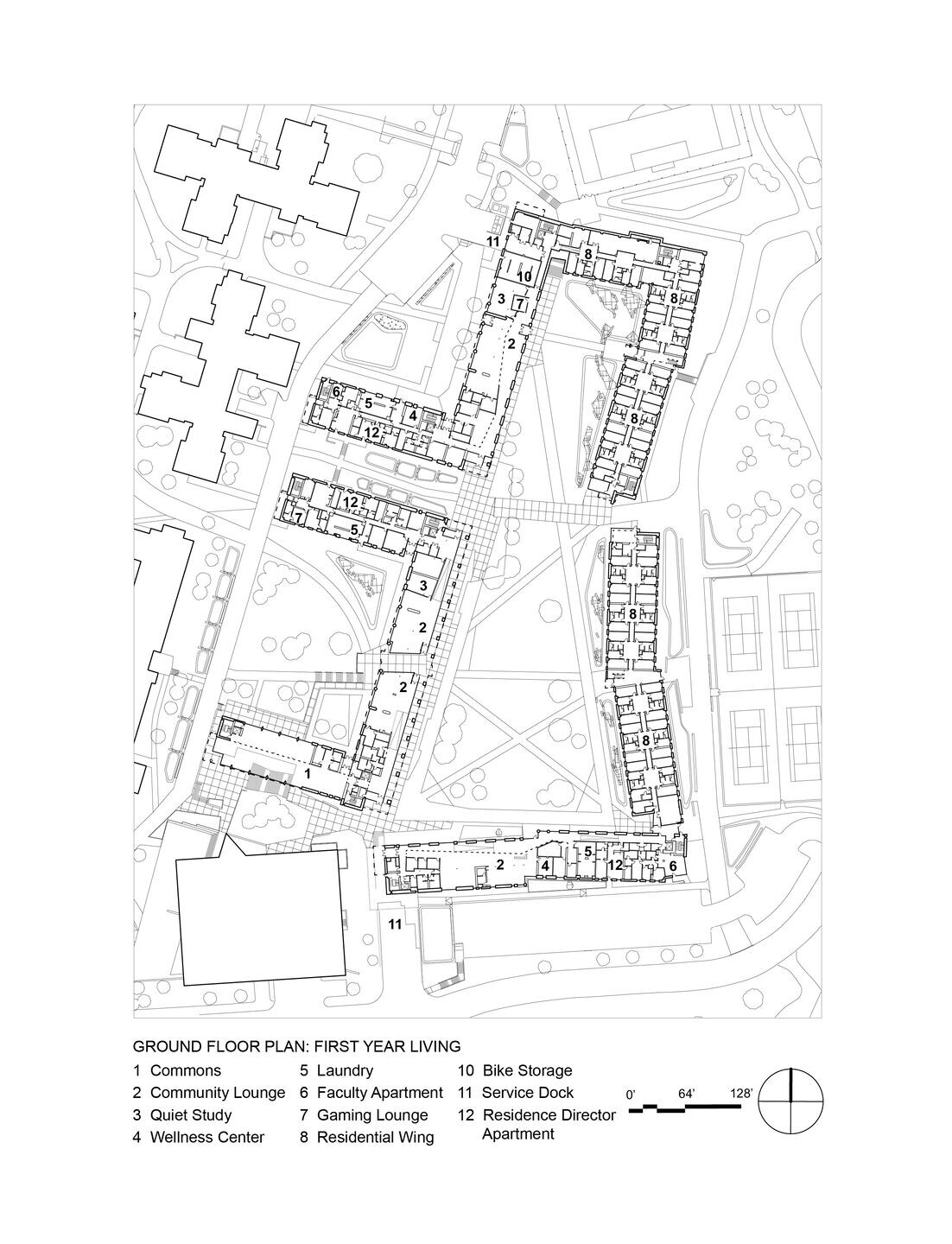